How Robotics is Transforming Manufacturing
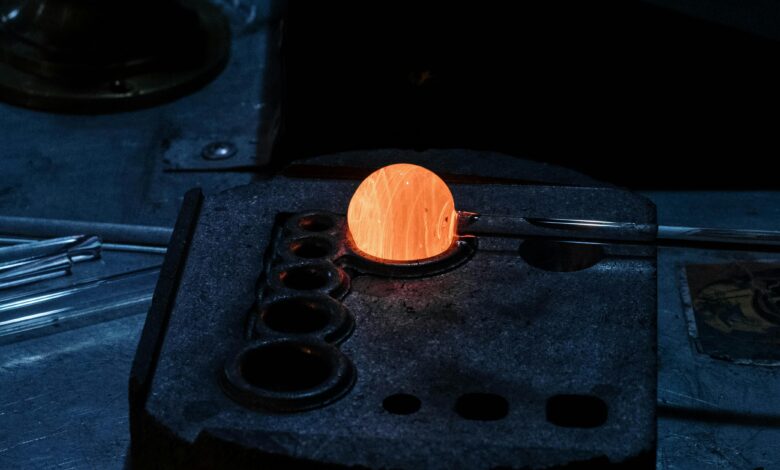
The manufacturing industry has undergone a profound transformation over the past few decades, driven largely by advancements in robotics and automation. From automotive assembly lines to electronics production, robots are now integral to modern manufacturing processes. They enhance efficiency, improve precision, reduce costs, and enable manufacturers to meet the demands of an increasingly competitive global market. In this article, we’ll explore how robotics is reshaping the manufacturing landscape, its benefits, challenges, and future trends.
The Role of Robotics in Modern Manufacturing
Robotics refers to the use of programmable machines that can perform tasks autonomously or semi-autonomously. In manufacturing, these machines are designed to handle repetitive, dangerous, or highly precise tasks that would otherwise require significant human effort. Here’s how robotics is being applied across various stages of manufacturing:
1. Assembly and Production
Robots excel at assembling products with speed and accuracy. For example:
- Automotive Industry : Robots weld car frames, install components, and paint vehicles with unmatched consistency.
- Electronics Manufacturing : Robots assemble tiny parts like circuit boards and microchips, which require extreme precision.
2. Material Handling
Robots streamline material handling by moving raw materials, work-in-progress items, and finished goods throughout the facility. Examples include:
- Automated guided vehicles (AGVs) and autonomous mobile robots (AMRs) transporting materials between workstations.
- Robotic arms picking and placing items on conveyor belts or into storage systems.
3. Quality Control and Inspection
Robots equipped with sensors, cameras, and AI algorithms inspect products for defects more accurately than humans. This ensures higher quality standards and reduces waste.
4. Packaging and Palletizing
Robots automate packaging processes such as boxing, sealing, labeling, and stacking pallets. This not only speeds up operations but also minimizes errors.
5. Customization and Flexibility
Advanced robotics enables mass customization, allowing manufacturers to produce personalized products efficiently. Collaborative robots (“cobots”) work alongside humans to adapt quickly to changing production requirements.
Benefits of Robotics in Manufacturing
The integration of robotics into manufacturing offers numerous advantages:
1. Increased Efficiency
Robots operate continuously without fatigue, significantly boosting productivity. Tasks that once took hours can now be completed in minutes.
2. Enhanced Precision
Robots deliver consistent results with minimal deviation, ensuring high-quality output even for complex tasks.
3. Cost Savings
While the initial investment in robotics can be substantial, long-term savings come from reduced labor costs, lower error rates, and improved resource utilization.
4. Improved Safety
By taking over hazardous tasks—such as heavy lifting, welding, or working with toxic substances—robots protect workers from injuries and health risks.
5. Scalability
Manufacturers can scale production up or down easily by adjusting robotic workflows, making it easier to respond to fluctuating demand.
6. Sustainability
Robots optimize energy consumption and minimize material waste, contributing to greener manufacturing practices.
Challenges of Implementing Robotics in Manufacturing
Despite their many benefits, the adoption of robotics in manufacturing comes with challenges:
1. High Initial Costs
Purchasing, installing, and maintaining robotic systems can be expensive, especially for small and medium-sized enterprises (SMEs).
2. Technical Expertise
Operating and maintaining advanced robotics requires specialized skills, which may necessitate additional training or hiring experts.
3. Job Displacement Concerns
Automation has raised fears about job losses in traditional manufacturing roles. While new jobs are created in areas like robot programming and maintenance, there is still concern about workforce displacement.
4. Integration Complexity
Integrating robotics into existing systems can be challenging, particularly for older facilities with outdated infrastructure.
5. Cybersecurity Risks
As factories become more connected through IoT-enabled robots, they become vulnerable to cyberattacks. Protecting sensitive data and ensuring system integrity is critical.
Key Technologies Driving Robotics in Manufacturing
Several cutting-edge technologies have accelerated the adoption of robotics in manufacturing:
1. Artificial Intelligence (AI)
AI-powered robots can learn from experience, adapt to new situations, and make decisions independently. For instance, AI-driven vision systems allow robots to identify defective products during inspections.
2. Machine Learning
Machine learning algorithms enable robots to optimize their performance over time based on real-time feedback and historical data.
3. Internet of Things (IoT)
IoT connects robots, machines, and sensors across the factory floor, enabling seamless communication and real-time monitoring of production processes.
4. Collaborative Robots (Cobots)
Unlike traditional industrial robots, cobots are designed to work safely alongside humans. They are smaller, more flexible, and easier to program, making them ideal for SMEs.
5. 3D Printing and Additive Manufacturing
Robots equipped with 3D printing capabilities can create prototypes and custom parts on demand, reducing lead times and material waste.
Future Trends in Robotics and Manufacturing
As technology continues to evolve, several trends will shape the future of robotics in manufacturing:
1. Smart Factories
The concept of Industry 4.0 envisions fully automated “smart factories” where robots, AI, and IoT collaborate to optimize every aspect of production. These factories will feature predictive maintenance, real-time analytics, and self-correcting systems.
2. Human-Robot Collaboration
The line between human and machine work will blur further as cobots take on more sophisticated tasks. Humans will focus on creative problem-solving and decision-making, while robots handle repetitive or physically demanding jobs.
3. Edge Computing
Edge computing allows robots to process data locally rather than relying on cloud servers, reducing latency and improving responsiveness in time-sensitive applications.
4. Sustainable Robotics
Manufacturers will increasingly adopt eco-friendly robotics solutions, such as energy-efficient designs and recyclable materials, to align with sustainability goals.
5. Modular Robotics
Modular robots consist of interchangeable components that can be reconfigured for different tasks. This flexibility will make robotics accessible to a wider range of industries.
Real-World Examples of Robotics in Manufacturing
Example 1: Tesla
Tesla uses advanced robotics extensively in its electric vehicle production lines. Robots handle everything from welding and painting to battery assembly, enabling Tesla to achieve rapid production rates.
Example 2: Amazon
Amazon employs thousands of robots in its fulfillment centers to sort, pack, and transport goods. These robots work alongside human employees to fulfill orders faster and more efficiently.
Example 3: Foxconn
Foxconn, a major supplier for Apple, has deployed tens of thousands of robots to assemble electronics. The company aims to automate up to 80% of its manufacturing processes.